Renewables
Renewables
Sustainable Top Union
To alleviate the environmental impact of global warming and extreme weather conditions, zero emissions and carbon neutrality have become popular topics. Worldwide, there is an active transition towards achieving zero emissions and developing renewable energy sources. Top Union, too, is no exception. Through the establishment of renewable energy infrastructure, such as solar photovoltaic power generation systems, and the replacement of old equipment with new ones, Taiwin enhances energy efficiency and functionality. Through proactive strategies and advanced deployment, Top Union pioneers new opportunities in the green wave of a low-carbon economy.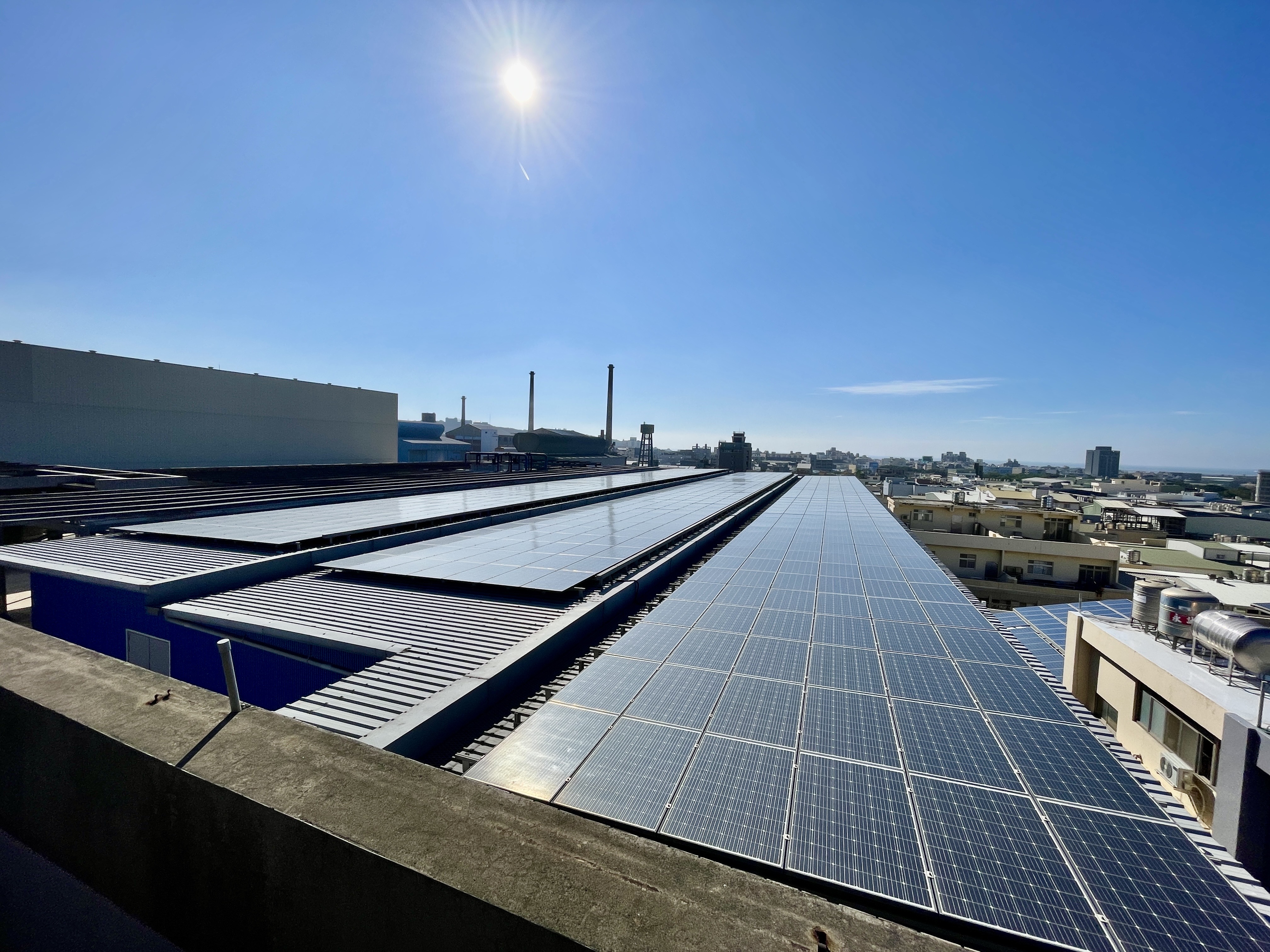
Renewable energy
Solar Photovoltaic Power Generation
In recent years, renewable energy has flourished. Renewable energy can be regenerated in a short time, and the conversion process into energy does not produce other pollutants. Taiwin Electronics actively implements the construction of renewable energy facilities, assisting in the installation and connection of commercial operation generators under the Energy Bureau's third category of renewable energy power generation equipment application. By establishing solar photovoltaic power generation systems, the total power supply can reach up to 500 KWh/Hr, reducing carbon emissions from traditional coal-fired power generation and achieving energy self-sufficiency.The installation of solar panels on rooftops not only reduces indoor temperatures with shading and heat insulation effects but also decreases the electricity consumption of air conditioning, contributing to energy conservation and carbon reduction.
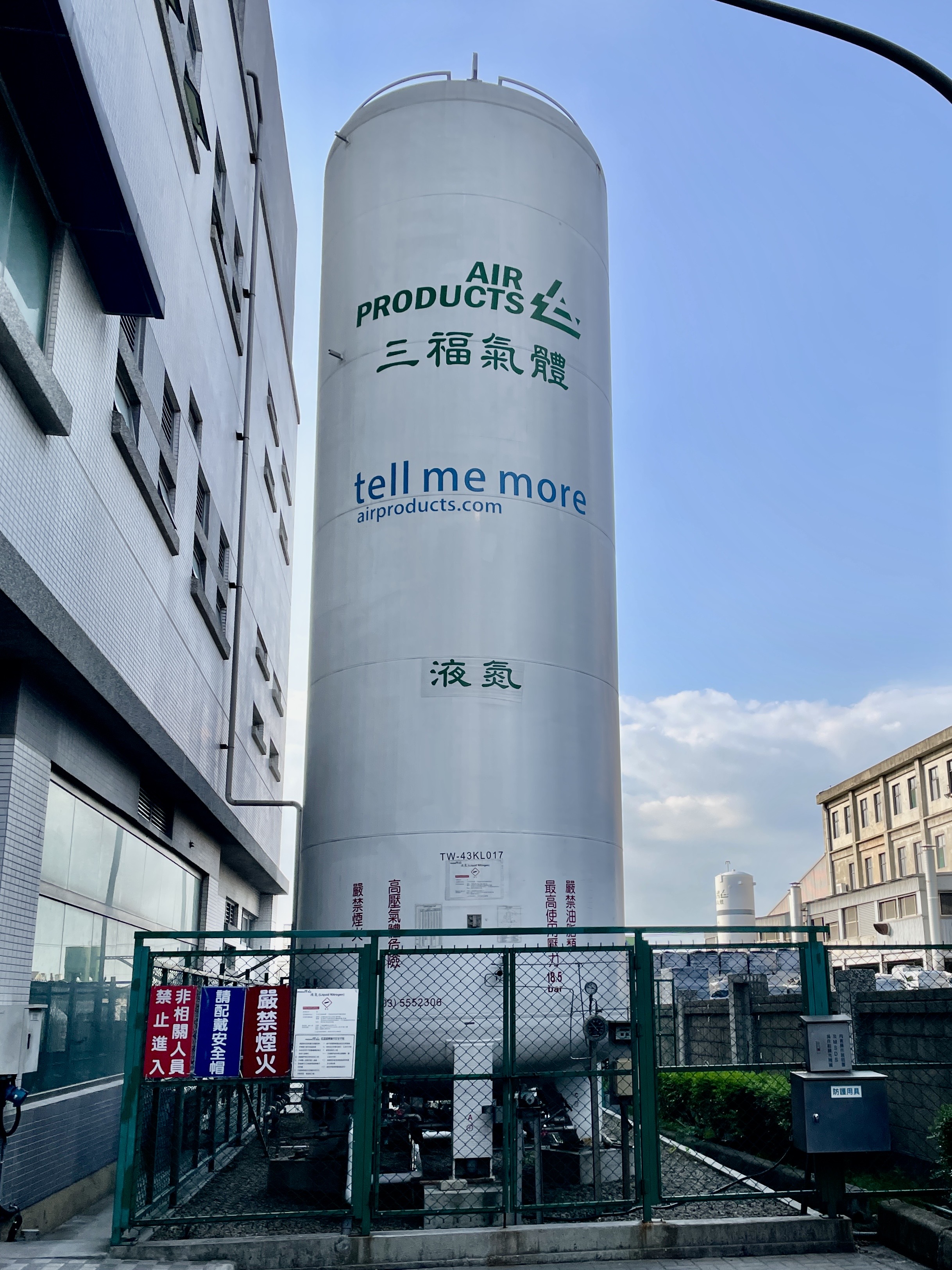
Nitrogen Gas
A liquid nitrogen supply system is established, replacing the old nitrogen generation machine model. This change saves over 100 KW of electricity per month and eliminates maintenance costs. With larger gas storage tanks, the liquid nitrogen supply system has a more stable gas supply mode and higher gas purity, exceeding 99.999%. Through the replacement of old equipment and the introduction of different technologies, energy conservation and carbon reduction are achieved, providing a more stable, abundant, and better-quality service to the production line.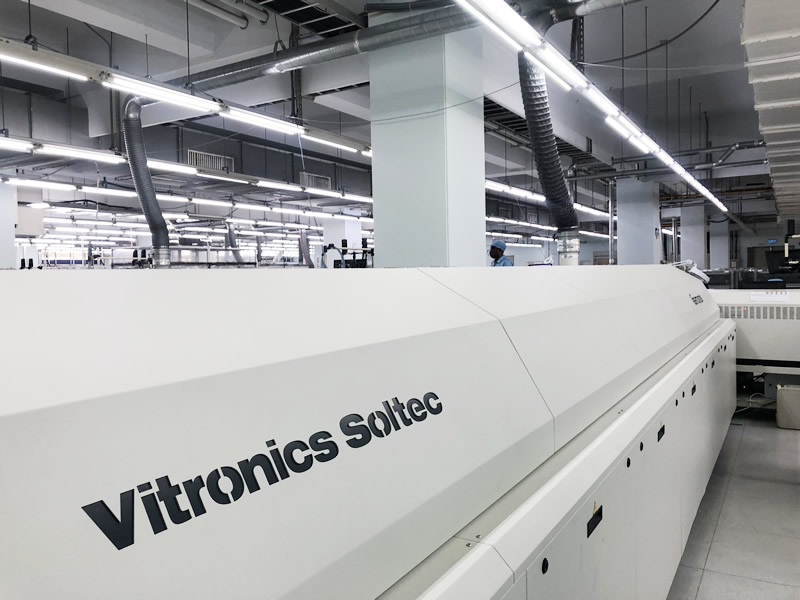
SMT Equipment
Placement Machine:
Improves production line efficiency (synchronously produces two types of circuit boards), uses dual-track models for high-quality quality (checks component issues, circuit board warping issues), and diversifies production (supports various components, handles various PCB sizes).
Printing Machine:
Accurate and efficient line changeover.
Inspection Machine:
High-speed, high-precision resolution (high-precision imaging system).
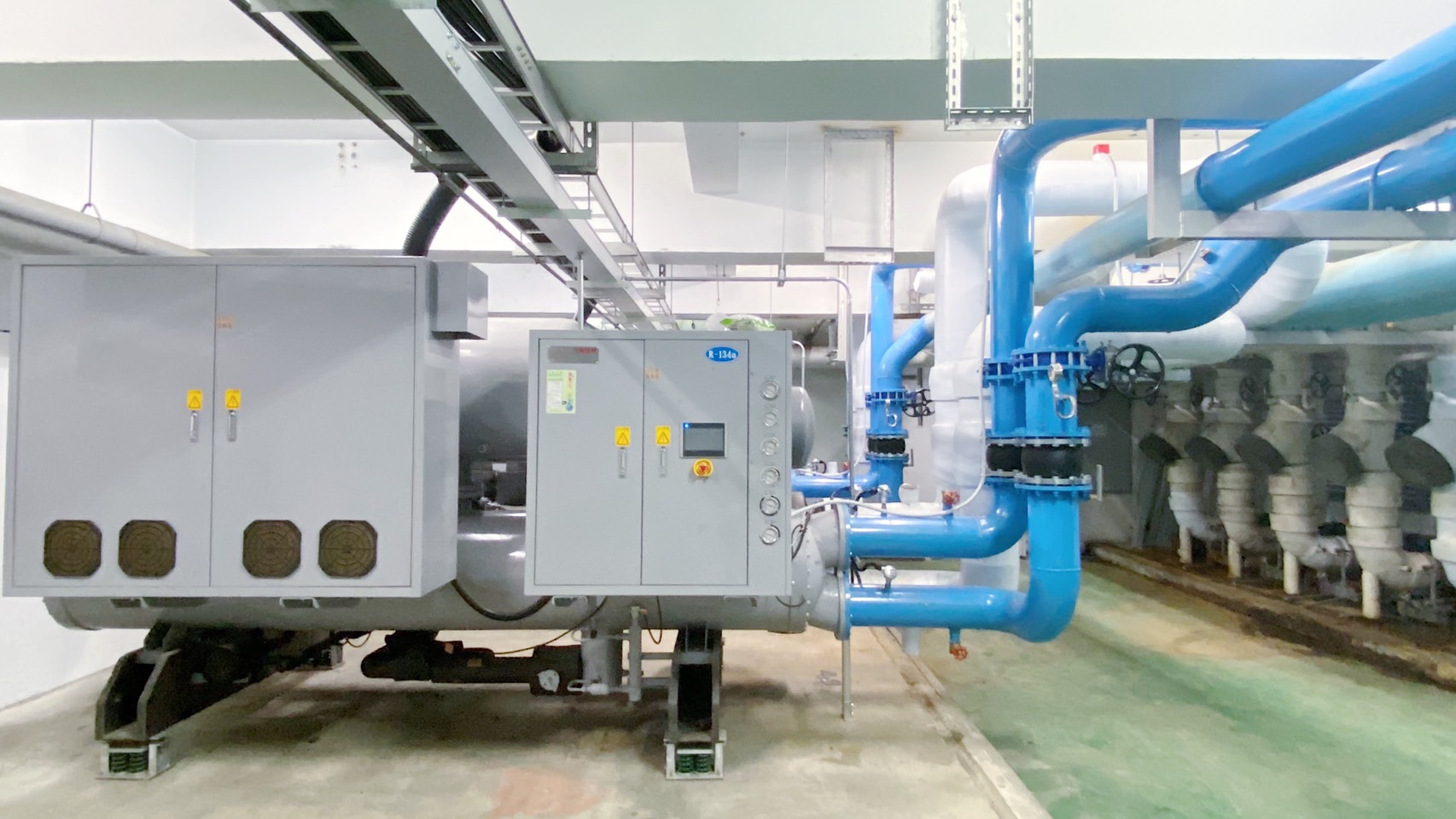
2024 Equipment Upgrade — Chiller
Current Status:
- The current chiller system in the plant is equipped with two fixed-speed screw chillers, both manufactured in 2005 and in operation for 18 years. The power consumption is 236.6kW, with an initial efficiency of 0.79kW/RT. Considering an annual cooling capacity degradation of 1.5%, the current capacity is approximately 228RT, and the current efficiency is 1.04kW/RT. These units have been identified as needing improvement.
- The current water pumps have efficiencies below IE1, resulting in low efficiency.
- There is no monitoring system in place, and all operations are manual, which prevents real-time operational status information from being provided. Data recording for equipment operation and energy-saving control for air conditioning is also unavailable.
Improvement Measures:
This project is included as a major investment for the year, involving the upgrade of chiller equipment and auxiliary water pumps, along with the installation of a new monitoring system:
The project scope includes:
- Replacing the existing two fixed-speed screw chillers with first-class efficiency equipment.
- Replacing auxiliary cooling water pumps with IE4 efficiency pumps.
- Installing an air conditioning monitoring system, covering chillers, chilled water pumps, regional pumps, cooling water pumps, and cooling towers.
Expected Outcomes:
- Annual electricity savings of over 750,000 kWh.
- Annual CO2 reduction of over 300 tons.